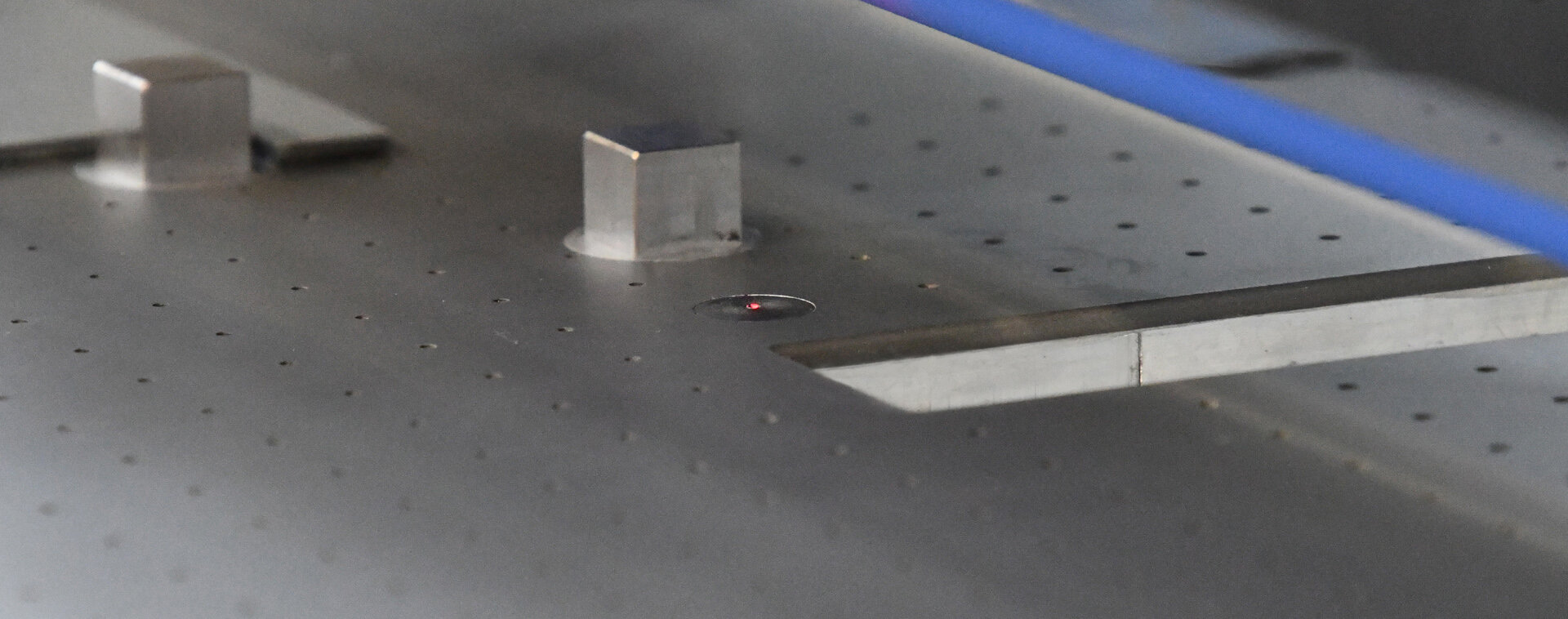
Components and Options
Specific printing processes for individual customer requirements
Printing Systems
Components and options
Thieme applies its many years of experience in the development and implementation of individual machines in accordance with customer requirements. The customer with his/her specific printing process is brought to the foreground and included in every step of development.
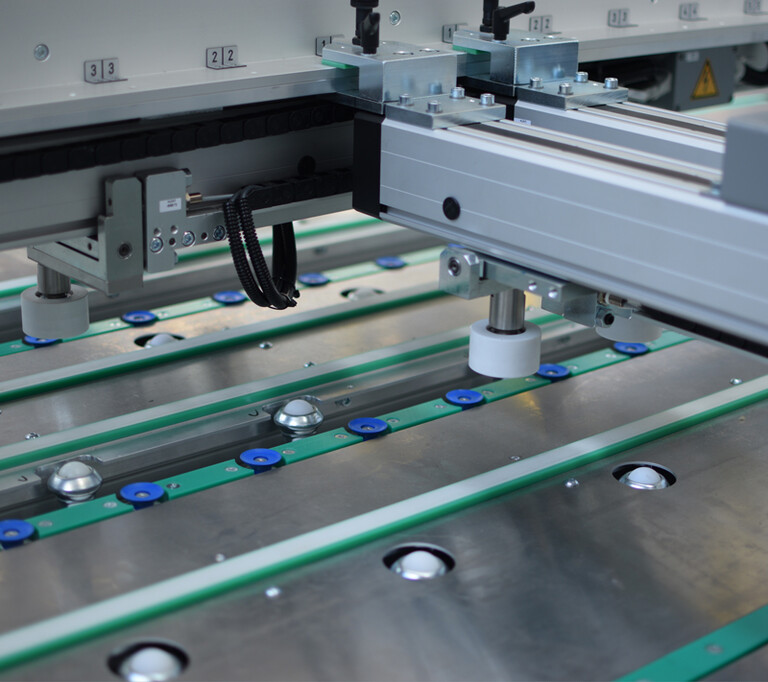
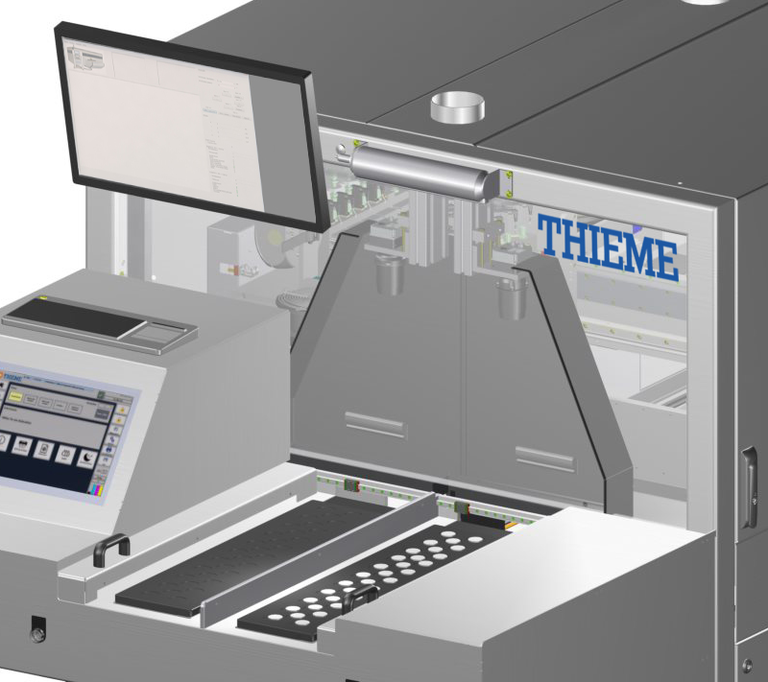
Components
Digital Image Alignment
for digital printing machinesA perfect print result is not possible without precise positioning of the printed material - until now. With Thieme's Digital Image Alignment automatic alignment system, substrates can be fed to the press in random positions. Advantages: time savings, less waste, more efficiency in automated printing processes.
The contours and/or an angle-indicating feature of the reproduced image has to be learned in a one-time teach-in process. When changing products, a trained operator will need no more than one extra minute per image to set up the digital alignment, the rest of the printing process is fully automated.
Once the teach-in ends, the actual production process can begin. When the substrate is loaded and an object with the learned contours is identified on the printing table, the software aligns the assigned layout with the object in perfect register. A new print file is automatically generated containing information on the object’s positioning along with the layout placed on top of it. A raster image is then produced, and the machine immediately starts printing.
There are essentially no limits to substrate shape or material.
As soon as a substrate arrives on the printing table, it is scanned for edges and contours. Other features may be used to identify the positions of substrates that are hard to align mechanically: coins, flat injection-molded parts with irregular contours or asymmetrically shaped panes of glass. For round substrates, the contour has to be supplemented with an eccentric feature in order to clearly determine the angular position.
Different substrates can also be automatically printed in parallel as long as they have been taught in. In other words, substrates with different geometries and features can all be loaded on the printing table and printed in a single print cycle. The system will flag non-taught-in substrates as defective and refuse to print them, preventing misprints caused by loading incorrect parts.
THIEME Digital Image Alignment is available for all Thieme digital printing solutions, which includes various combinations of inks and printheads.
Components
Laying and stacking
Automation not only reduces costs but also ensures high process reliability. In-line and off-line system concepts for the most diverse substrates are designed to meet customer requirements and implemented for laying and stacking in a way that is gentle on the material. A wide variety of variants matched to the transfer to/from the printing stations.
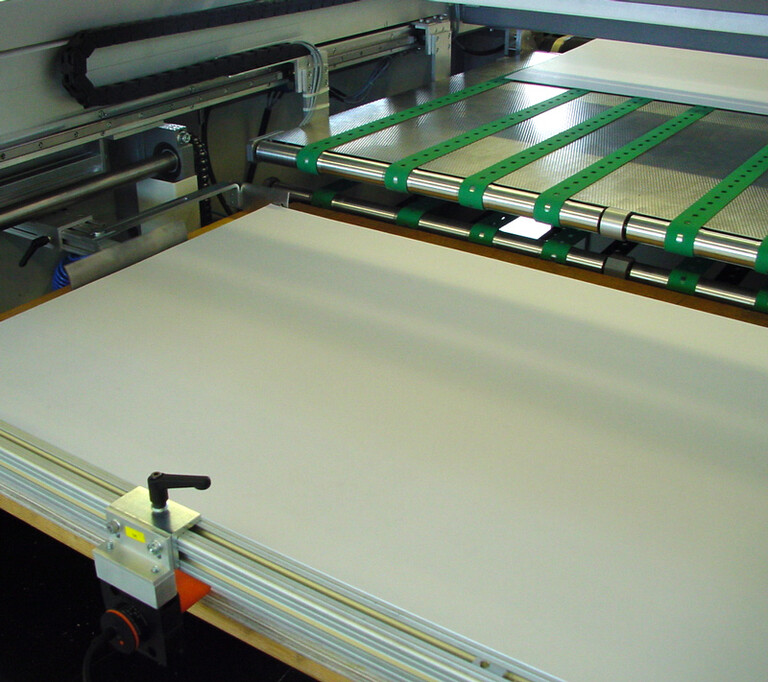
- Handling which is gentle on the material
- Industrial environment
- Customized designs
- Handling which is gentle on the material
- Customized designs
- High outputs
- Standard solutions available
- Proven technology
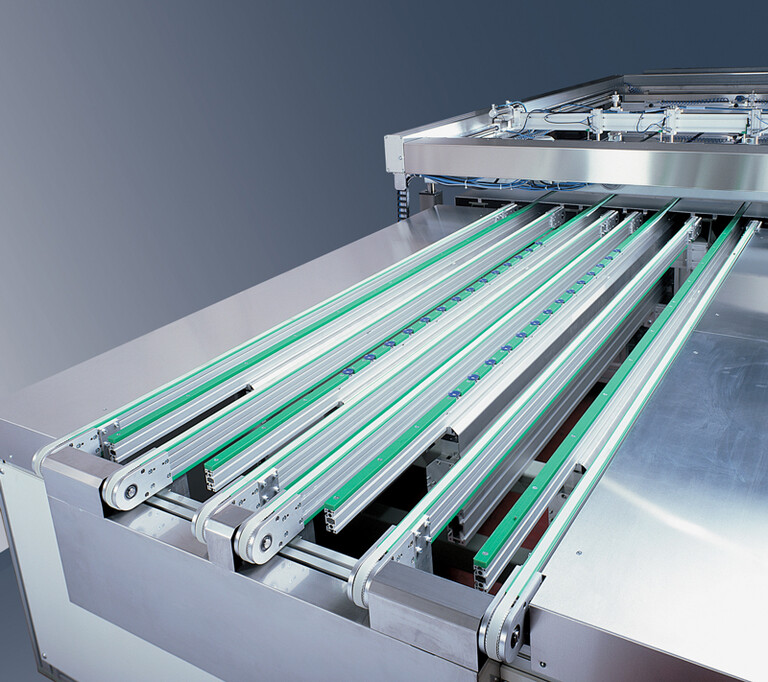
Components
Conveyer technology
Thieme develops and builds conveyor technology for a large number of flexible and rigid printing materials. This technology focuses on feeding the printing materials to the printing and drying processes.
Transport routes with belts, rollers or conveyor transport, optionally with changes in the transport direction and/or rollers without directional change.
The consolidation of multiple substrates for efficient utilisation of the drying route.
Change in the transport direction of the substrate by 90° or 180°
Parallel running substrates are reduced to one web.
Substrates can be removed from a stack before printing or can be stored in a stack after printing.
To adapt to the printing speed or the rhythm of further processing, the distance between the individual substrates can be changed.
Components
Dryer technologies
Drying is an important component of the printing process and should also be matched to the application.
Thieme collaborates with prominent manufacturers in the area of dryer technology and will be happy to advise you on how to achieve optimal process coordination. The modular design makes it possible to achieve numerous combinations.
Two important topics in this area are the reduction in energy consumption and heat recovery. The latest technologies offer added value such as a reduced payback period.
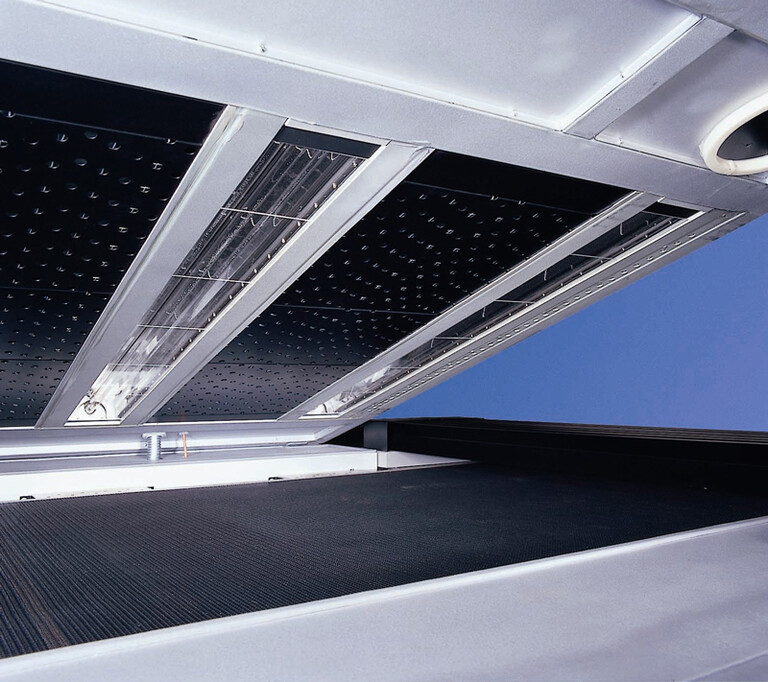
They operate as continuous dryers using a combination of high-pressure hot air and medium wave infra-red radiation. Based on a modular design, the dryers can be supplied for every application in accordance with the customer requirements.
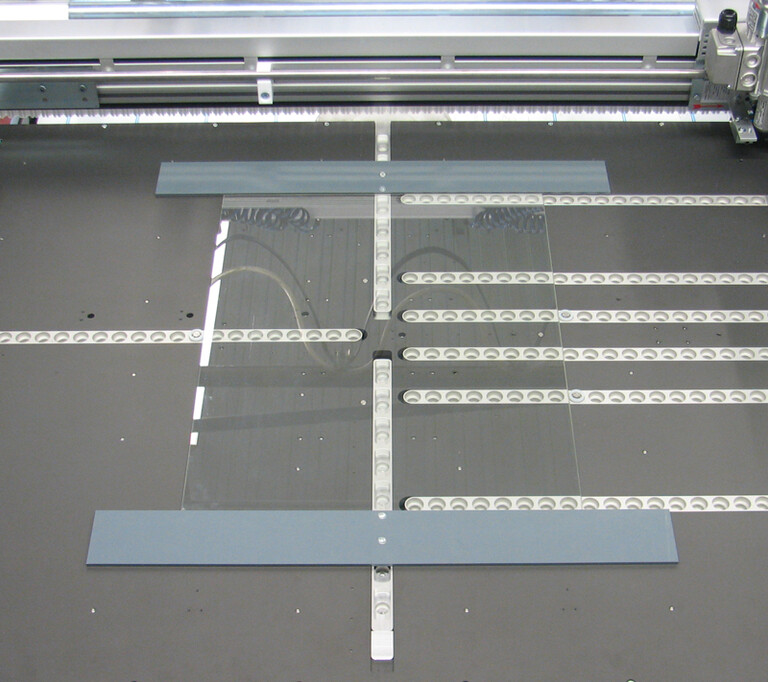
Components
Substrate arrangement
The substrates for many printing processes must be precisely fitted to the print. Depending on its type and application, the substrate can be aligned in various manners.
Two basic types of alignment are generally used — an optical alignment by means of a camera system or sensors and a mechanical alignment for the substrate edge or by the usage of pilot pins when register holes are punched.
Components
Cleaning and ionizing
Reliable and gentle removal of dust and other particles from surfaces is an important condition for the production of high-quality printed materials when screen printing or digital printing is used for printing or coating. Surface cleaning thus represents an important step in the printing process.
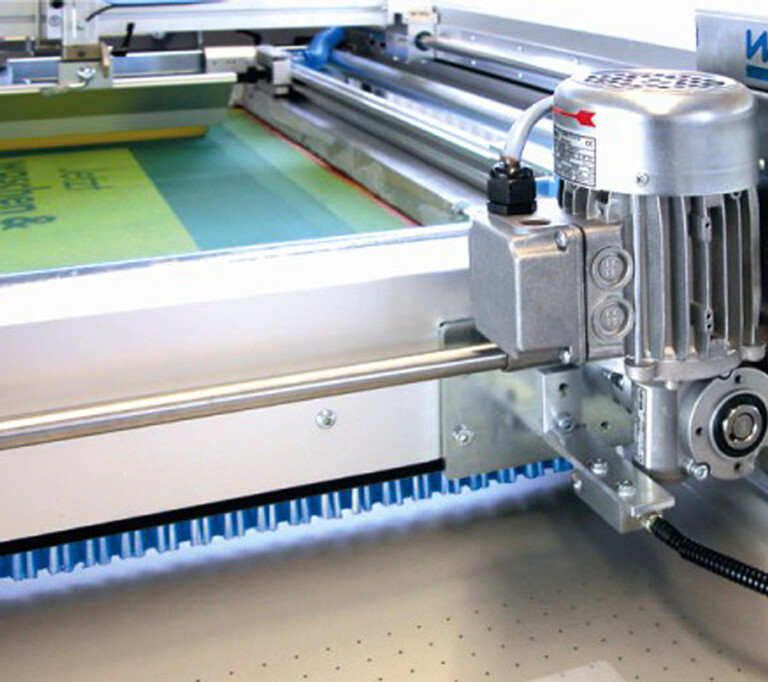
Benefits:
- Cleaning of surfaces contaminated by dust and particles
The particular advantage is the consistently high cleaning quality, even in cases of high particle contamination, without sacrificing the quality of the printed material being cleaned
Removal of static charges from surfaces - Process reliability at a consistently high level
High machine availability
Low operating and follow-up costs - Also possible for large printing widths of up to 3300 mm
Mounting on the print table:
- Combination of air and brush technology Cleaning systems for the graphical and industrial surface cleaning of flat surfaces in the form of plates, foils, paper and cardboard.
- An additional option is the cleaning with highly efficient elastomer and adhesive rollers. This results in a considerable reduction in production rejects, which could be caused by dust and particles on flat plates or plastic foils.
Malfunctions and production stoppages due to static charges are prevented by targeted discharging and thus increase the efficiency and productivity of the printing processes. The targeted elimination of static charge ensures a flawless material flow of the printed materials whereby trouble-free sheet transport can be guaranteed within the print line. This not only improves the printing process, but is also an optimal condition for further processing.
Benefits:
- Cost-reducing performance increase
- Reduced downtimes and stoppage times
- Higher production speeds are possible
- Better printing quality
- Reduced coating time
- Optimal usage of the Thieme printing machine
- Reduced consumption of inks, printing materials and cleansers
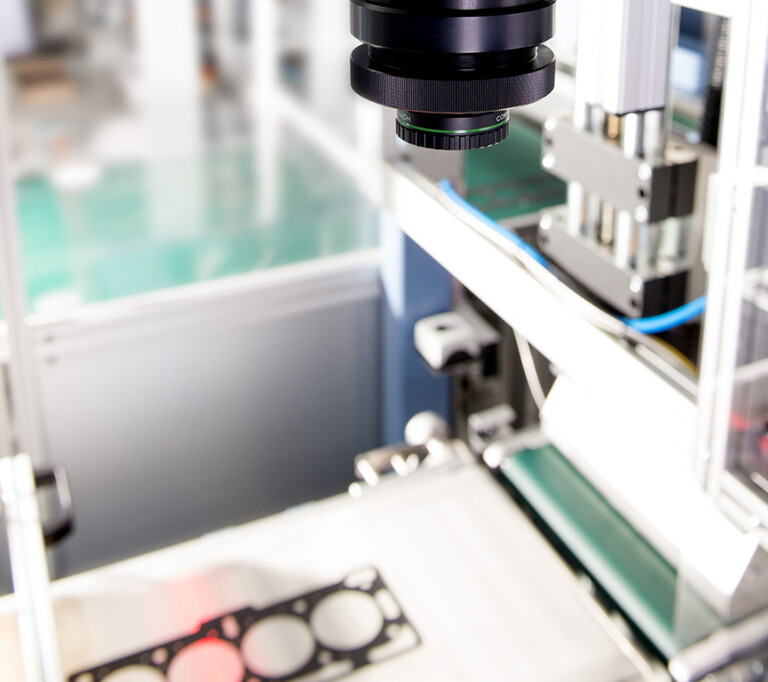
Components
Control
There is currently a strong trend in screen printing and digital printing towards automation and industrialisation. New standards are being set in the area of product quality control.
Print-Inspection-Systems no longer require manual monitoring activities but rather perform a reliable and integrated quality check.
- Inspection concepts tailored to each customer - Error classification is possible
- Documentation of the quality check and archiving
- Integration of inspection systems for production monitoring
- Multivariate Process control
Components
Set-up and alignment
Thieme offers innovative options for time savings, the implementation of high-precision printing, and job results which can be reproduced at all times.
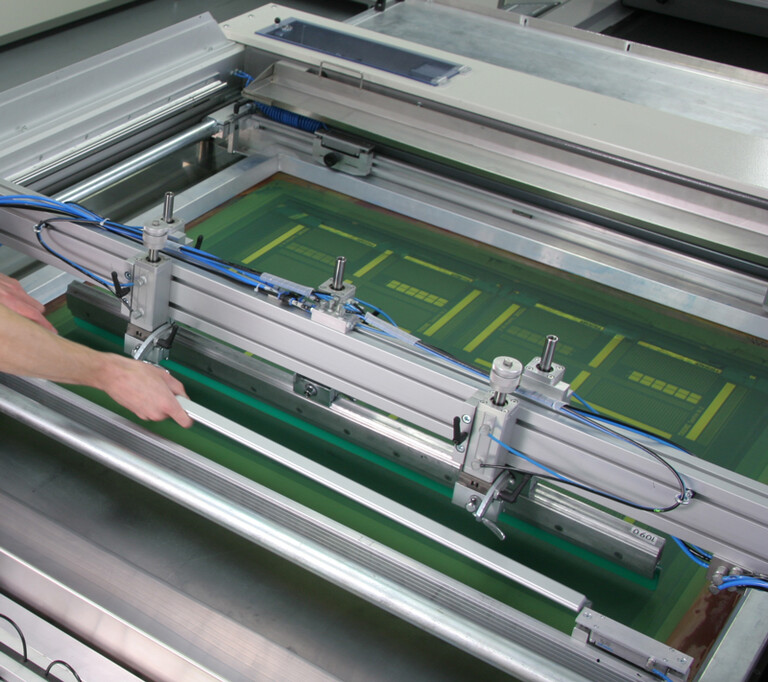
Thieme screen printing machines reflect its many years of experience in the graphic and industrial sectors Quick set-up, user-friendly design, program control with intelligent software, pneumatically operated functions. This all reduces the time consumed from print to print and print-run to print-run and enables the customer to print more efficiently.
- The Thieme alignment system for the shortest set-up times.
- Exactly aligned copies due to precisely punched mounting foils – colour for colour
- Screen change in just a few minutes due to automatic screen positioning using 2 CCD cameras
- Substrate alignment in just seconds using the automatic camera system. Highly precise automated alignment of the substrate using CCD cameras, evaluation software and monitors, including 3-axis servo motor positioning of the air-bearing print table
- Quick printing squeegee and flood squeegee replacement
- Pneumatically operating Thieme squeegee unit with self-alignment and sensitive printing control
- Quickly adjustable screen insert system with pneumatic clamping of the screen frames
- Programmable logic controller (PLC) considerably reduces the set-up times
- Reproducible job results and high operating reliability
- Visual system checks on the mounting pins for high-precision printing
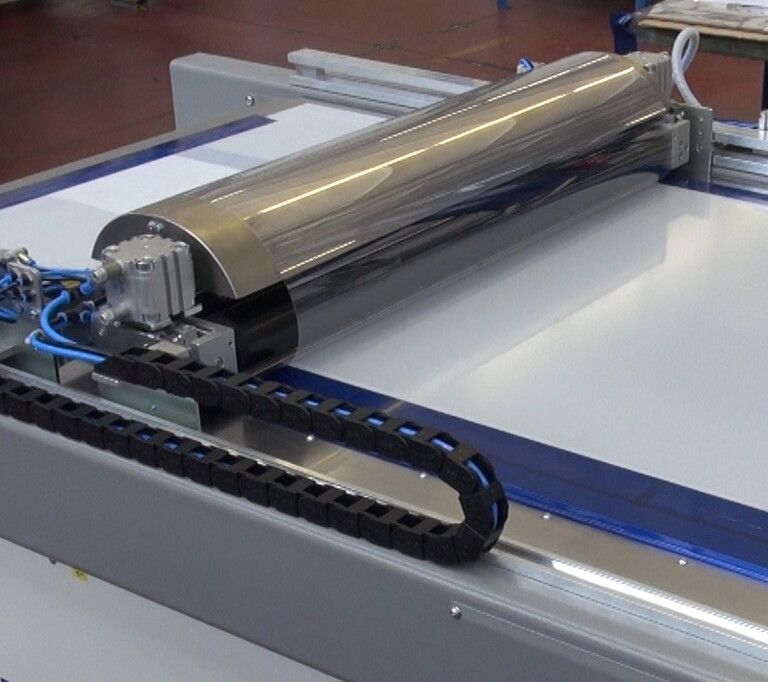
Components
Laminating
THIEME builds semi-automatic laminating machines for the cold lamination of spacer foils in various formats and thicknesses.
- e.g. Flexible sensors and electrical circuits
Components
Squeegee cutting
Increased print quality through excellent squeegee edge.
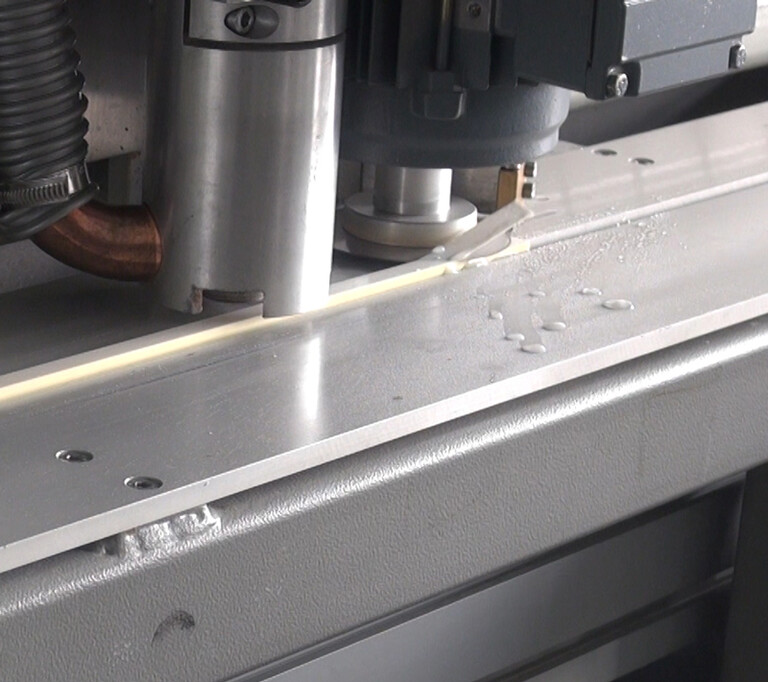